十堰专业生产大口径防腐螺旋钢管多少钱一吨格齐全
十堰大口径防腐螺旋钢管知识焊接。焊接工艺流程如下: 检查管材并清理管端→紧固管材→铣刀铣削管端→检查管端错位和间隙→加热管材并观察小卷边高度→管材熔接并冷却至规定时间→取出管材。在焊接过程中, 操作人员应参照焊接工艺卡各项参数进行操作, 而且在必要时, 应根据天气、环境温度等变化对其进行适当调整:<br> ①核对欲焊接管材规格、压力等级是否正确,检查其表面是…
十堰大口径防腐螺旋钢管知识 焊接。焊接工艺流程如下: 检查管材并清理管端→紧固管材→铣刀铣削管端→检查管端错位和间隙→加热管材并观察小卷边高度→管材熔接并冷却至规定时间→取出管材。在焊接过程中, 操作人员应参照焊接工艺卡各项参数进行操作, 而且在必要时, 应根据天气、环境温度等变化对其进行适当调整: ①核对欲焊接管材规格、压力等级是否正确,检查其表面是否有磕、碰、划伤, 如伤痕深度超过管材壁厚的10% , 应进行局部切除后方可使用; ②用软纸或布蘸酒精清除两管端的油污或异物; ③将欲焊接的管材置于机架卡瓦内, 使两端伸出的长度相当(在不影响铣削和加热的情况下尽可能短,宜保持20——30mm) , 管材机架以外的部分用支撑物托起, 使管材轴线与机架中心线处于同一高度, 然后用卡瓦紧固好; ④置入铣刀, 先打开铣刀电源开关, 然后再合拢管材两端, 并加以适当的压力, 直到两端有连续的切屑出现后(切屑厚度为0.5——10mm, 通过调节铣刀片的高度可调节切屑厚度) , 撤掉压力, 略等片刻,再退开活动架, 关闭铣刀电源; ⑤取出铣刀, 合拢两管端, 检查两端对齐情况(管材两端的错位量不能超过壁厚的10% , 通过调整管材直线度和松紧卡瓦予以改善; 管材两端面间的间隙也不能超过0.3mm(de225mm以下)、0.5mm(de225mm——400mm)、1mm(de400mm以上),如不满足要求,应在此铣削,直到满足要求。 ⑥加热板温度达到设定值后,放入机架,施加规定的压力,直到两边小卷边达到规定高度时,压力减小到规定值(管端两面与加热板之间刚好保持接触,进行吸热),时间达到后,松开活动架,迅速取出加热板,然后合拢两管端,其切换时间尽量缩短,冷却到规定时间后,卸压,松开卡瓦,取出连接完成的管材。 三、焊接工艺参数与焊接直接有关的参数为:温度、时间、压力。焊接工艺曲线图表示为焊接过程压力与时间的关系图。
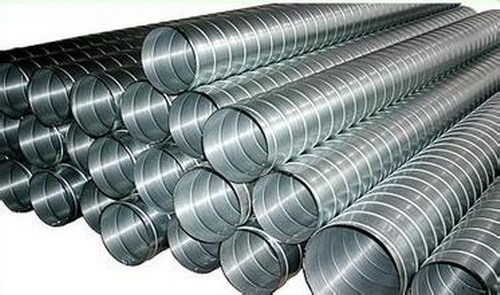
十堰大口径防腐螺旋钢管新闻 厚壁螺旋钢管的质料边部处理 国外较遍及选用铣边机作质料边部处置,以保证边部质量和契合技术需求的几许形状。铣边机价钱昂贵,单机价钱在1200万美元以上,且维护费用和运转本钱都很高。技术所选用专用刨边机对质料作特别边部处置,待质料进入成型机组后,在翅片成型孔经过加大挤压力,将边部处置到适宜形状,保证焊接挤压力。这样的组织能在满意技术需求的前提下,将设备出资降低到铣边机的1/15,运转本钱也仅仅铣边机的1/5。 厚壁螺旋钢管的质料边部处置质量,是完成管坯杰出成型的关键因素之一。按API标准规定,在大型油气输送管道中,当通过高寒地带、海底、城市人口稠密区等1类、2类地区时,直缝埋弧焊管是唯一指定适用管型。按成型方式不同又可分为: UOE焊管:单张钢板在边缘预弯后,经U成型、O成型、内焊、外焊、机械冷扩径等工序; JCOE焊管:即按"J-C-O-E"预焊、成型、焊接后经冷扩径等工序; HME焊管:由芯棒滚压法按"C-C-O"成型、焊接后经冷扩径等工序。
螺旋钢管专业生产厂家,公司坚持“诚信经营,品质营销,力求多赢”的市场运作理念,正确的经营思路,给公司带来了良好的经济效益,为网络化营销打下了良好的基础。秉持务实进取的精神,我公司力创业内第一品牌,更期待与广大用户共享辉煌未来!
十堰大口径防腐螺旋钢管简介
烟囱烟道用螺旋钢管防腐方案 烟囱烟道用螺旋钢管的脱硫、除尘防腐是防腐中的难点,要求防腐材料同时要达到耐高温,耐酸耐碱,防腐蚀性好,防水防潮,耐磨抗冲击,表面光滑,不容易长生裂纹,膨胀系数好,不容易脱落等以上要求,这就选防腐材料时全面考核,严格审查,确保烟囱烟道脱硫、除尘防腐万无一失,长时间使用。
脱硫方法通常如下 : ①先将螺旋钢管、卷管表面除油去污,之后再进行除锈,除锈等级应满足不低于Sa2.0或St3标准。在锈面清理干洁后,用VEGF树脂打底,待干后施工。 ②用手工泥刀刮镘成1-2mm(每道)厚的VEGF胶泥层,数小时后即硬化,再按设计要求施工至规定厚度。一般在每涂1mm厚度时进行检测,以确认涂层是否有针孔及其它瑕疵。 ③在弯角或形状突变处适当增加厚度,或同FRP复合使用。 ④用VEGF树脂罩面一至二道。 ⑤VEGF鳞片胶泥涂层质量控制。VEGF鳞片胶泥涂层的质量好坏直接影响其耐腐蚀性能和使用寿命,因此应对VEGF鳞片胶泥涂层的质量加以严格控制。一般情况下,涂层的终检测项目主要有:外观缺陷、硬度、针孔测试、厚度测试、锤击检查等。
|